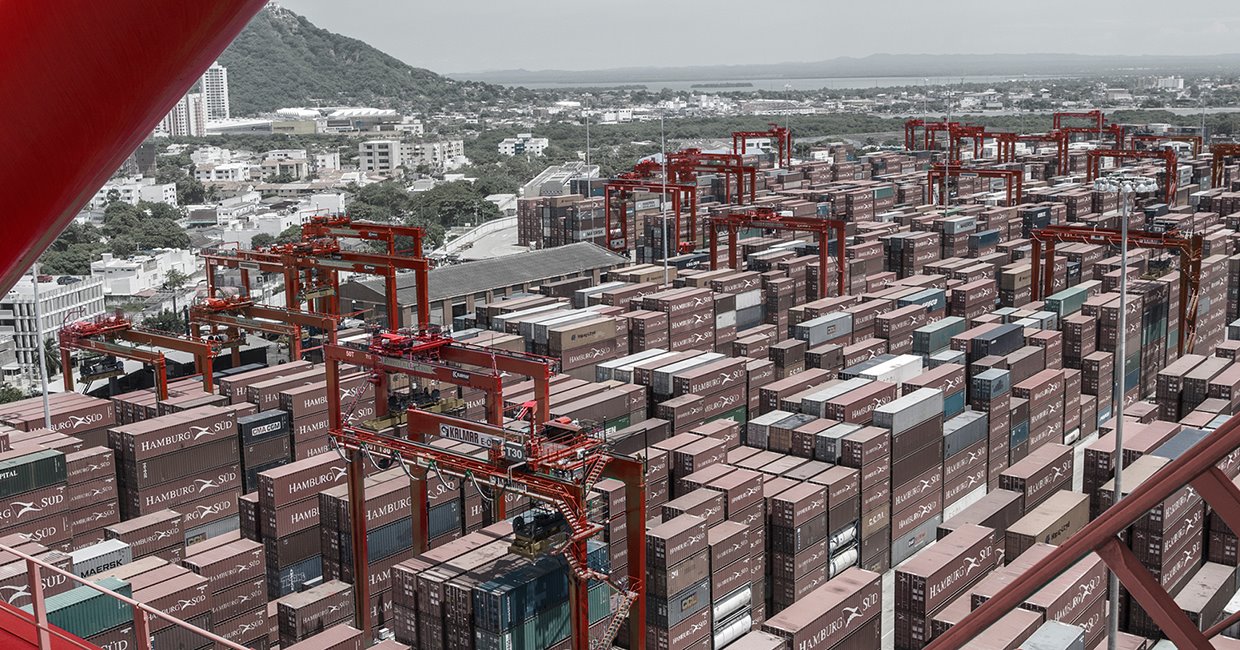
Designing the next generation container port
The Next Generation Container Port (NGCP) Challenge sought to identify innovative ideas on how to plan, design and operate the next generation of container ports that exemplify performance, productivity and sustainability.
This was an exciting challenge, as it was about a real business case: to design the biggest, the most efficient and most sustainable terminal in the world, which can be built in the coming ten years.
In Singapore, container terminals have developed a unique product of high service level at high transshipment volume, making it the world hub for container trade. For the coming decade, Singapore is looking into ways to make a quantum leap in container operations and logistics to retain its position. To this aim, the Maritime Port Authority of Singapore launched a worldwide Next Generation Container Port Challenge to design the future terminal for Singapore, which could be built in the next 10 years.
Kalmar’s proposal for the NGCP Challenge was prepared in close cooperation with Singapore Nanyang Technological University, APL Co Ltd, Fraunhofer IDM@NTU and VTT Technical Research Centre of Finland. Our focus was to understand the key performance indicators given by the organiser and the local context.
High ambitions
The key performance indicators (KPIs) of the NGCP Challenge were a combination of ambitions which might sound contradictory:
- high productivity (40 moves per hour)
- high service level (90% Berth on Arrival)
- high utilisation (more than 80,000 TEU per hectare)
- high transshipment rate (80%)
- high sustainability in environmental and financial terms
However, when reviewing these KPIs without any limitations of the past, we deemed them very well achievable. It’s no science fiction, taken into account that all concepts, solutions and technology must already clearly exist, as the terminal needs to be build within 10 years.
Starting from a clear understanding of the business needs and drivers of the future port and the local situation, including the weather and climate conditions, all technology and solutions in our concept were chosen because they contribute to achieve the KPIs of this challenge.
Our design
The major characteristics in our design of the next generation container port are:
- Intelligent terminal operating system (TOS), which includes planning at the last moment to achieve high flexibility in berthing
- Automation of the remaining manual tasks in the operational process to increase safety, efficiency and productivity
- No crossing of ‘lateral’ transportation of transshipment boxes and ‘perpendicular’ vessel operation boxes
- Opportunities for implementation of sustainable technology included during the design stage
- No administration, planning and control tower buildings in the terminal area
The concept of the two-type storage system includes a smaller size of automatic stacking crane (ASC) and the system of a central yard to support other main functions of the terminal operation. This provides possibilities for a clearer management of different flows.
Further, to achieve the highest possible separation of the different modes of transport, an underground transport system with automatically guided vehicles (AGVs) was chosen to connect all the ASC stacks. This is a simple tunnel system with opening at the landside area of an ASC stack. The system can pick up and lower containers on an AGV arriving underneath the openings.
The waterside operation (image above) is supported by shuttle carriers to achieve high productivity and minimum number of vehicles, with an average of 2.5 shuttles per crane sufficient to achieve at least 40 moves/hour in crane operations. The quayside will have one uniform type of crane, which will be able to handle vessel sizes of 18,000 TEU and above. The crane driver will operate the quay cranes remotely since the cranes will be operated at a very high trolley speed. This arrangement will provide high berth flexibility.
To further support a short cycle time and safe operation, all delaying factors in the crane-cycle process will be removed by implementing certain solutions and logistic choices in horizontal transport. These include automatic container number recognition, automatic twistlock, auto profiling of containers on ships, automatic container status registration of damage claims, automatic crane cycle at land-side (dual trolley) and use of shuttle carriers to facilitate de-coupled operation.
Separation of transshipment traffic from the vessel operation
The cycle time and driving distance of a shuttle carrier is very short. The implementation of charging stations near the ASC stack will allow a fast charging of the small battery every time the shuttle carrier docks at the ASC stack. A minimum number of vehicles can be kept when using shuttle carriers. This will result in a much less dense traffic in this area, allowing a smoother traffic control without delays.
For transshipment logistics, our design goal was to separate the transshipment traffic flows from the vessel operation. This will lead to high vessel productivity and a high-speed, smooth and safe operation. In our design, the transshipment containers can be transported in three ways:
- Hot connection for vessels already waiting at other berth. The transfer is done with a limited number of trucks in the manual lane under the cranes. This lane is also used for off-standard containers and project cargo.
- Short-term transshipment for containers to be received by vessels arriving within a short period of time. These boxes are transferred directly by AGV from one ASC stack to another by means of an underground tunnel connecting all ASC stacks.
- Long-term transshipment where the containers will be stored in the central storage yard and transported to another location by shuttle carriers driving on a central alley in the central spine of the terminal.
The underground transportation system is one of the innovative ideas of our proposed concept (image above). The transportation at different levels will eliminate crossing of traffic flows. As discussed previously, the challenge in design of next generation container port is to achieve high service and high productivity of vessel handling and at the same time to handle a high volume of transshipment in the terminal. A simple tunnel network located on the central axis of the terminal, connecting all the ASC stacks, is used for moving transshipment boxes across the terminal. The equipment used for moving boxes in the underground system has a simpler design and functionality than full-fledged AGVs. This is due to the very dedicated function, dedicated tracks and simpler navigation.
The central yard with the transshipment movements as well as its interface with the waterside stacks and the hinterland trucks is shown in the image below.
The central yard will support the management and transportation of the transshipment boxes. Cantilever rail-mounted gantry cranes (RMGs) are the main equipment for the central yard. In the central alley between the central storage blocks, a closed transportation area with two loading lanes and two driving lanes deals with the movement of transshipment boxes.
Automation helps maintenance
The frequency and need for maintenance will be significantly reduced in this terminal since most equipment is fully automated or supported by automatic functions, such as optical routing, soft landing and collision avoidance.
All equipment will be equipped with a real-time data collection system to monitor the status of vital components.
All the ideas and solutions in this future terminal are existing or on the development radar of several suppliers. I certainly believe that this terminal can be build with limited risks and is financially very sustainable, as no complex technology or infrastructure have been chosen to achieve the next level of service and performance.
Related articles
Further reading
Subscribe and receive updates in your email
Iscriviti alle nostre pubblicazioni