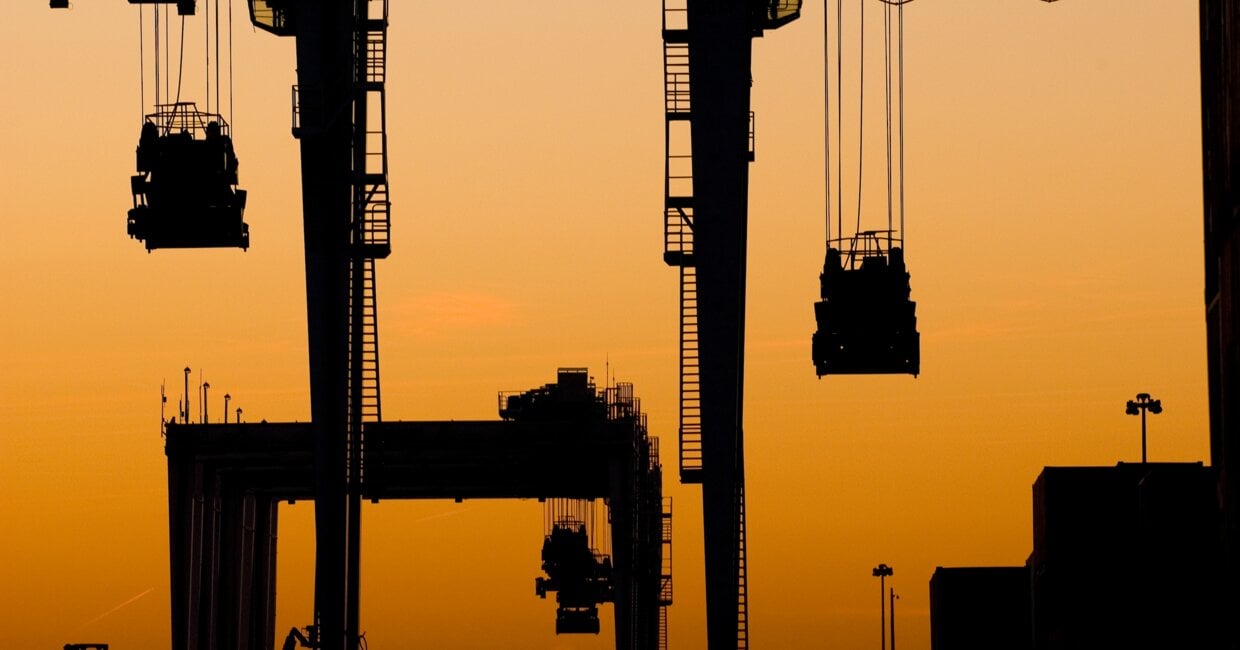
Cutting fuel consumption, emissions and noise with the latest evolution in hybrid RTG technology
As the drive to improve environmental performance at container terminals continues to gather pace, operators are faced with several choices when it comes to expanding or renewing their rubber-tyred gantry (RTG) crane fleets in order to achieve sustainability gains. Hybrid RTG drivelines have developed significantly in recent years, offering even greater gains in fuel efficiency and reductions in emissions and noise. Kalmar is now proud to introduce its second-generation hybrid RTG – a highly fuel-efficient machine that makes no compromises on performance.
While vessels and road trucks are the most significant sources of air pollution at container terminals, sustainable hybrid solutions for container handling can help operators reduce their airborne and noise emissions significantly while reducing both fuel and maintenance costs at the same time. Hybrid technologies are a particularly attractive alternative to fully electric drivelines in markets where the quality and reliability of the electricity supply may be poor, or at terminals where the existing infrastructure may not support a cable-reel or bus bar setup.
The new Kalmar Hybrid RTG builds on the proven, sustainable performance of the previous-generation model to deliver even greater savings in fuel efficiency, airborne and noise emissions, and maintenance costs.
The latest in battery and regenerative energy technology
The super-capacitor system of the previous model has been replaced by the latest lithium-ion (Li-ion) battery technology, which has a much higher energy-storage capacity. The Li-ion battery, which comes with a five-year guarantee, is combined with a smaller diesel power unit, which is not only highly fuel-efficient – consuming up to 50% less fuel than a conventionally powered RTG – but also quieter and easier to maintain.
Just like the previous-generation model, the new Kalmar Hybrid RTG features a regenerative energy system that stores energy generated by braking and spreader-lowering for later use.
The gains in terms of fuel efficiency and lower maintenance requirements can be explained in extremely simple terms: the power unit’s running hours are significantly reduced because it is not used to power any of the crane functions, only to charge the Li-ion battery. Fewer engine running hours means less fuel consumed and less component wear. And with the battery doing all the work – powering the lifting and driving operations – noise emissions are also significantly reduced.
Greater savings in fuel efficiency, airborne and noise emissions, and maintenance costs.
Proven Kalmar quality and performance
Just like all our other RTG models, the Kalmar Hybrid RTG is a highly efficient and flexible platform that offers industry-leading performance levels and state-of-the-art features. These include an intuitive graphical user interface as standard as well as options such as an electro-mechanical anti-sway system, SmartProfile stack anti-collision system, and SmartView camera system. The Kalmar Hybrid RTG can be customized to meet the precise business requirements of each individual operator terminal in terms of height, width and cabin options.
No compromises on performance or sustainability
With its ability to cut the cost of every container move while also minimising environmental impact, hybrid RTG technology is a highly attractive option for many terminals around the world. The Kalmar Hybrid RTG combines the latest in Li-ion battery and diesel power-unit technology with Kalmar’s proven and flexible platform to deliver a machine that makes no compromises on performance or sustainability.
Related articles
Subscribe and receive updates in your email
Iscriviti alle nostre pubblicazioni