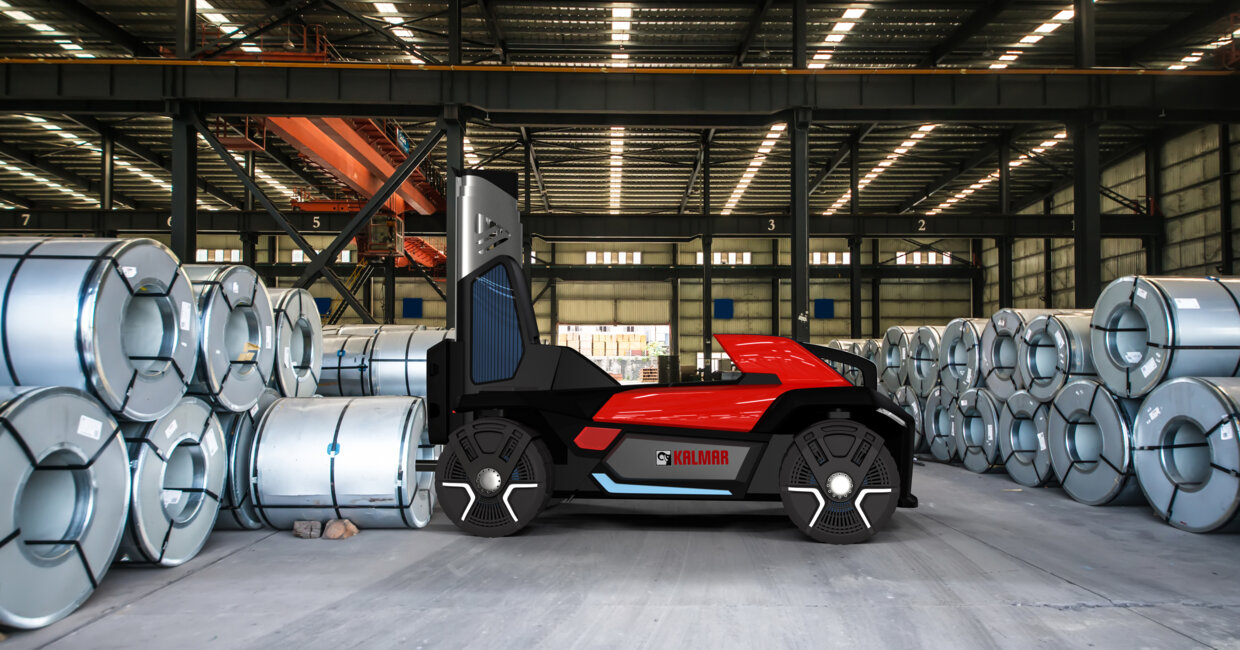
Getting past bottlenecks in industrial automation
Automating mobile material handling equipment provides interesting opportunities for heavy industry. First steps towards automated logistics have already been taken, and it is only a matter of time when it will become an everyday reality for all industrial companies.
Over the years automation has cut production costs radically in most fields of industry and has become indispensable. In heavy industry, however, even fully automated production tends to start and end with drivers moving goods with mobile equipment. How to create feasible end-to-end automation solutions for industrial logistics?
Variety of goods instead of standardised containers
Fully automated container terminals demonstrate that it is possible to successfully automate logistics even with heavy loads. However, terminal solutions are made to lift and move loads of predefined shapes, sizes and weights on fixed paths and in fenced areas. This is rarely the case in heavy industry.
In an industrial setting, mobile material handling equipment move in a mixed environment where machines drive freely across the plant yard among other vehicles and pedestrians to pick up and drop off goods at various sites. In many cases, the driver needs to get out of the cab to secure the load.
Because of the different settings, automating logistics in heavy industry requires adaptation of not just the logistics but various other processes as well. Also the environment, such as the plant yard, warehouses and traffic routes, need to be taken into account in planning the solution.
Kalmar studies indicate that automation is best introduced in most industrial environments by starting with select sequences of the logistic flow, within limited physical areas, and then gradually expanding the scope. The change also requires new types of machines.
Towards autonomy via sophisticated driver assistance
In a fully automated container terminal, a centralised equipment control system, TLS, coordinates the traffic, and mobile machines execute based on orders they receive, whereas in an industrial environment such as logistic support in for example a saw mill or steel mill, a more decentralised approach is needed. Even when performing predefined tasks, individual forklift truck needs to figure out on their own what to do when facing unexpected loads or other trucks on unexpected paths.
Kalmar approaches automation development of mobile equipment step by step. First requirement is electricity, and that is why Kalmar has stated to offer electrically powered versions of all its mobile equipment by 2021.
Another important step involves developing and applying sophisticated driver assistance systems with cameras, radars and other sensors. These are used to improve safety and reduce the risk of damaging goods even when applied to present-day logistics operations. By collecting data from sensors installed in manually driven equipment and sending it to Kalmar cloud for further analysis, Kalmar is able to feed information to develop autonomous equipment.
On the road to automating logistics applications in heavy industry, we see partly remote-controlled equipment as a natural step, until automated logistics will be managed by an equipment control system. But in the end all processes should be connected to the overall process automation system in the plant.
Where do you see the biggest bottlenecks in automating your logistics processes?
Peter Söderberg
VP Offering Development, Kalmar
Related articles
Further reading
External resources
Subscribe and receive updates in your email
Iscriviti alle nostre pubblicazioni