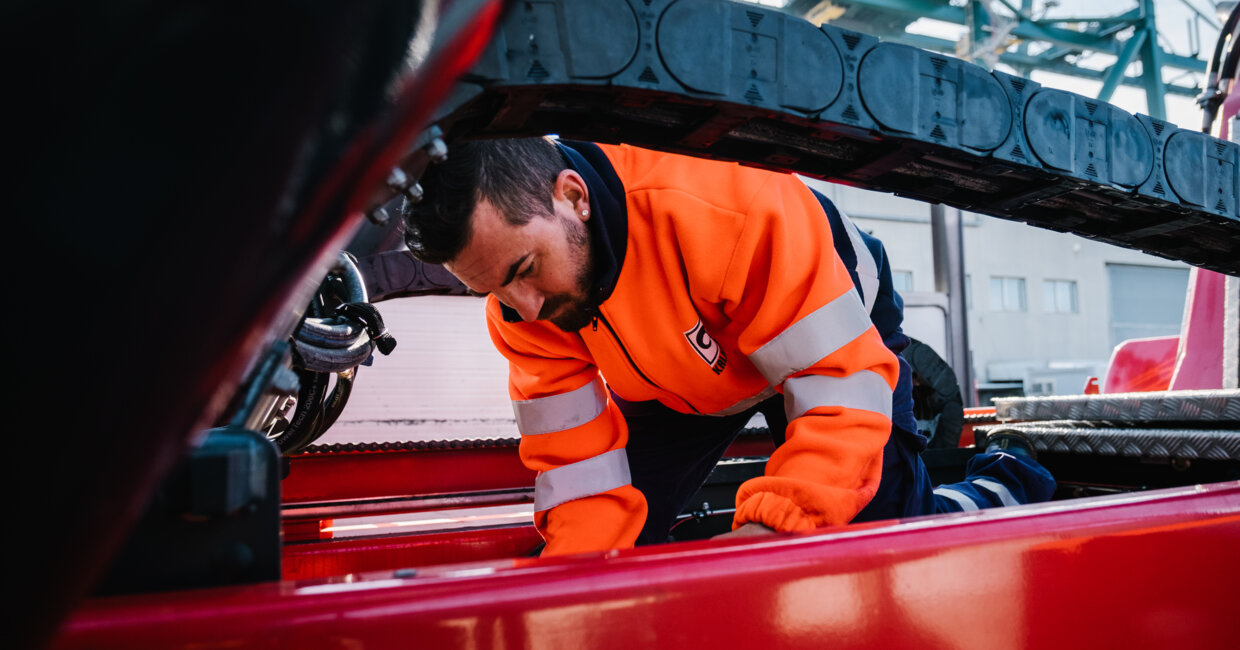
How to ensure the safety of the equipment
The coronavirus pandemic is a reminder of the symbiotic relationship between operator and machine safety. With global supply chains under unprecedented pressure, Kalmar local service experts are working tirelessly to ensure everyone is able to do their job safely and efficiently.
Hanna Kosunen, Product Portfolio Manager, Services and Sergio Peralta, Country Director, Kalmar Spain outline some of the steps customers can take to ensure their equipment is available and safe to use in these challenging times.
Good personal hygiene is the key
There are two main reasons why equipment safety is of particular importance now. Firstly, employers need to protect the health of their workers and secondly, they must ensure equipment is available for use at a time when internal resources may be stretched.
Companies need to ensure operators are maintaining good personal hygiene, this is the foundation for the safety actions against the virus/pandemic. High touch surfaces such as steering wheels and dashboards must be cleaned regularly and social distancing may necessitate changes to shift patterns.
“Operators have an important role to play in identifying the status of their machines by inspecting each machine before the start of every shift,” says Kosunen. “Operator feedback should be shared with operations and maintenance managers and issues reported using the checklist feature in Kalmar Insight.”
This operational checklist feature is particularly useful since it can be configured for every machine in a fleet - whether or not that machine was supplied by Kalmar.
Once the operator has started their shift it is important to note that they might be under more stress than normal due to factors such as health concerns, financial worries or infection of family members. Where resources limitations mean less experienced operators are being deployed they should be given additional support - including training where appropriate.
“Operators have an important role to play in identifying the status of their machines by inspecting each machine before the start of every shift."
Importance of preventive maintenance
Companies should also consider fitting additional safety features that ensure operators are wearing seat belts at all times, machines are operating at lower maximum speeds and/or colleagues in close proximity can see and hear approaching machines.
“The effects of close-downs and the crisis are varying depending on the company, but preparing the equipment to meet the operational needs and minimize the downtime remain vital,” adds Kosunen. “Inspecting the equipment, carefully planning the needed repairs in advance and adhering to preventative maintenance schedules is particularly important when fewer employees are available for work.”
Collecting basic equipment data automatically through the Kalmar Insight performance management tool provides a single view of the entire fleet and generates automatic alerts when maintenance is due. All this will help understanding the fleet status easier and make maintenance planning more proactive and flexible.
Kalmar has implemented a number of protocols to protect its service technicians from coronavirus.
“For example, our 460 service technicians in Spain must use gloves, face masks and protective glasses,” explains Peralta. “No more than two technicians are allowed in the same vehicle at any time and they must wear personal protective equipment, while protocols have been established for disinfecting not only machinery but also service vehicles, premises and tools after every shift.”
“With the help of our global spare part logistics network, we will explore all options for ensuring customers get the parts they need.”
New documentation to train employees
Kalmar is in daily communication with its clients in Spain and elsewhere to reassure them that it is taking all the necessary precautions to protect customers’ employees as well as its own.
“In Spain we are utilising both internal and external resources to develop documentation that can be used by site supervisors and managers to train employees individually or in small numbers on the new protocols,” says Peralta. “This documentation is regularly updated with the latest guidance from local and national authorities.”
One of the issues that customers have been particularly interested in since the start of the pandemic has been spare part management.
“Customers should reach out to their usual Kalmar contact to check the availability of any parts required for imminent maintenance and to plan ahead to support proactive maintenance with the needed spare parts,” concludes Kosunen. “With the help of our global spare part logistics network, we will explore all options for ensuring customers get the parts they need.”
Checklist: How to better ensure the safety of the equipment
- Ensure operators maintain good personal hygiene, for example washing their hands before and after each shift
- Clean high touch surfaces such as steering wheels and dashboards regularly
- Conduct machine inspections before the start of each shift and share results with operations and maintenance managers
- Consider fitting additional safety features to help operators who might be under more stress than normal
- Continue to adhere to preventative maintenance schedules
- Collect data automatically from the fleet for more proactive and flexible maintenance planning.
- Use your regular Kalmar contact to check the availability of any parts required for imminent maintenance
Hanna Kosunen and Sergio Peralta discussed safety issues relating to cargo and material handling operations during a webinar hosted by Kalmar in May – a recording of the webinar is available at https://www.kalmarglobal.com/news--insights/webinars/safety-first/
Related articles
Subscribe and receive updates in your email
Iscriviti alle nostre pubblicazioni