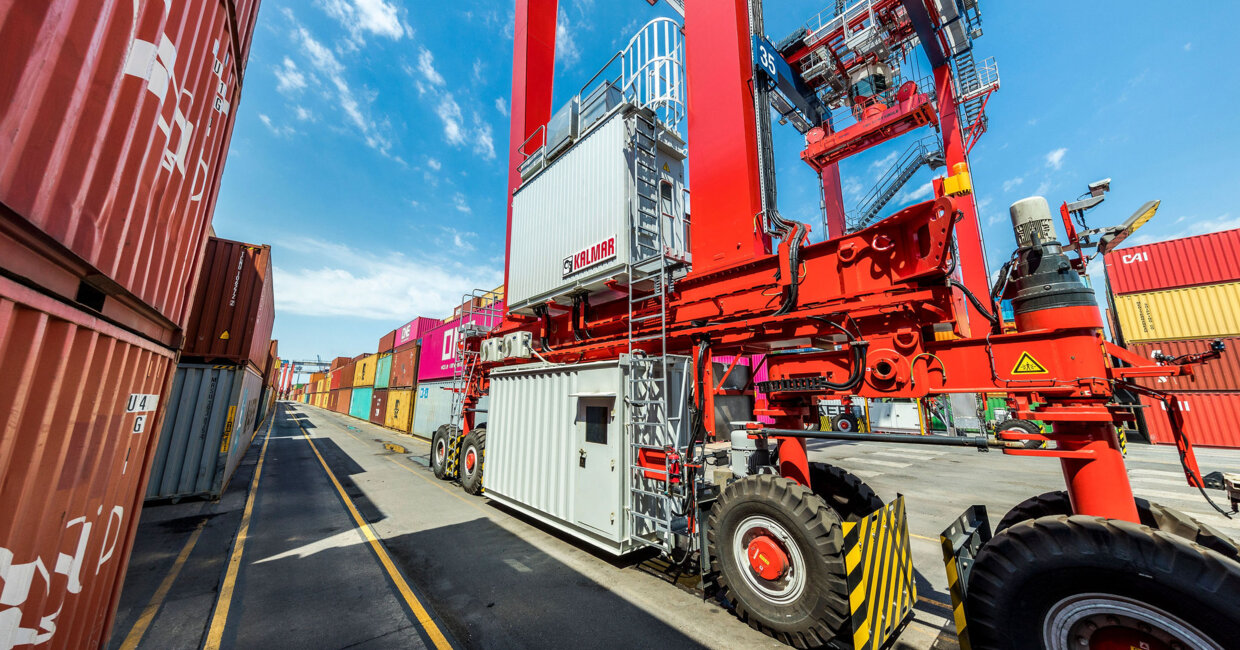
Kalmar Expert Roundtable (Part 2): How to address on-site emissions at ports & terminals?
Kalmar's Timo Alho, Jason Gasparik, Christopher Saavedra and host Pilvi Tähtinen-Sfakiotakis continue their discussion on enabling eco-efficient operations at container terminals. Check out part 1 here.
Last time, we talked about the overall industry landscape and the drivers that are steering terminals towards eco-efficiency. A crucial part of this is controlling the on-site emissions at ports and terminals. What can operators do to address them?
Christopher Saavedra, Manager, Terminal Design Services, Kalmar: It's crucial to understand the main sources of emissions at the terminal, which could be the vessels, the handling equipment, trucks or trains, among others. Having said that, terminals need to focus on what is under their control, so they are going to be looking mostly at the container handling equipment and how they can reduce the CO2 emissions from those.
Timo Alho, Director, Product Management, Kalmar: Terminal operators have many sources of information where they can start looking at this. Typically, the container handling equipment is the easiest place to begin. Every terminal knows the amount of fuel they use per year. Or if they aren't tracking this, they should be, and the fuel consumption can of course be converted directly to tons of CO2.
Then, if you want to drill down deeper, you start logging the operating hours of the equipment, maybe the number of handled containers, kilometres driven, and so on. That will give you some parameters that will enable you to analyse your CO2 footprint per container move. And once you are measuring something, you can start taking actions to reduce it. And of course, modern systems already provide a lot of information that you can use right away.
As Christopher said, the container handling is one part of the equation, but then you have external trucks operating in the terminal, which are more challenging to measure. For these emissions, maybe you don't get the exact measurements in kilograms of CO2, but you still have parameters that help you to start reducing them. For example, you can link truck turnaround times directly to the CO2 footprint that they generate. Likewise with the vessels; the faster you can turn around the ship, the shorter the time it stays in the terminal and therefore the lower the emissions during that period.
Jason Gasparik, Director of Sales, Ports & Terminals, Kalmar: That's a great point, because you might not be able to control the emissions of a 30-year-truck coming into your terminal. But you can control how long that truck queues at the gate to get into your terminal, how much time it takes to get their container, and then how fast it's out of the gate again. So as Chris said, you have to focus on what you can control and put aside the things that you can't, maybe addressing them later, when you're further down the path. Or you can try to find ways to influence indirectly the things that you can't control directly.
But it's important to remember this is a journey. It's not like you can just pull the trigger and everything will happen right away. It will take years, and you might not even have an exact end point in sight at this moment in time, but you have to start someplace, pick the low-hanging fruit and start moving forward. Then, two or three years down the road you reassess, you adjust, and you continue moving forward.
Especially in the United States, many terminal operators have moved from diesel-powered equipment to hybrids. What options are there for customers to choose from, when it comes to more eco-efficient equipment?
Jason Gasparik: One of the great things that I enjoy most about Kalmar is that we really have been a leader now for several years at the forefront of the technology in the industry, and we are working together with customers to really keep driving forward.
As of today, all of our straddle carriers, shuttle carriers, RTGs and all other yard cranes are already available as fully electric. And then you have the battery hybrid, which is a lithium-ion battery powered machine where the primary power of the machine is all coming from the batteries. So that enables us to use a much smaller diesel engine, and to only run the engine when we absolutely need to in order to recharge the batteries, which is a big difference from many of the other hybrid machines on the market and in other industries.
In my opinion, a true hybrid really should be defined as a machine that runs on battery power, and the engine is only switched on to recharge the batteries. You should not be using the engine to actually supplement power or anything like that.
Finally, of course we do have now the all-electric machines that are the strads, shuttles, the FastCharge machines and the RTGs that have been available in all electric and now come with batteries for cross-stack travel. So you can have locally emissions-free, fully electric strads, shuttles or RTGs. And there are so many advantages to these machines, from reduced maintenance costs to reduced noise pollution.
Actually, I think one of the biggest benefits of the hybrid machines is that they require absolutely no infrastructure to deploy. You can have a diesel-electric and hybrid straddle carrier sitting next to each other, and from 50 feet away literally nobody will be able to tell the difference. They look exactly the same and operate with exactly the same speeds and performance. The operator will notice the difference because the diesel engine is not running most of the time. So the machine is very quiet and of course the terminal operator will see a difference because the hybrid machines use less fuel, but no extra infrastructure is needed to deploy these hybrid machines, which is a really great thing.
What do terminal operators need to take into account when evaluating these different options? How can they arrive at the optimum solution for their specific operation?
Timo Alho: Indeed, it's never a "one size fits all" situation. A solution that is good for one terminal operator might not be suitable for another. Also, the terminal operations and the nature of the business will vary between terminals. You will see different operating scenarios, widely differing vessel sizes and so on. So all of this needs to be considered when building the operating scenarios.
Many needs are related directly to flexibility. For example, if you need to move a lot of your equipment around the terminal, maybe it's better not to invest in RTGs that are connected by cable reels. However, also the overall investment plans will be different from terminal to terminal, and operators need to consider the remaining lifetime of their existing equipment. So sometimes retrofitting electrification technology can be the better option if actually investing into completely new equipment is out of the question. Then there are the possible subsidies and grants that Jason mentioned. How do these tie into your financial strategy?
And finally, you also need to consider some very specific local conditions such as the quality of the electrical network. Is the power grid reliable enough to serve as the sole source of energy for all your equipment? In some locations, this can be a challenge, so fully electric might not be an option, but hybrid could be your best choice.
Jason Gasparik: Yeah. Many of our customers in, for example, South America are deploying hybrid cranes for exactly this reason. They want the benefits and eco-efficiencies of the all-electric or mostly electric crane, but they can't rely on the power grid 100% of the time. So they need to have the batteries and a small diesel engine.
Timo Alho: And the most important parameter in your business case is, of course, the price. The cost differential between the electrical power and diesel fuel will point very strongly towards whether you will need to go towards fully electric or diesel power with hybrid technology.
Read part 1 of the discussion here and stay tuned for the final episode.
Kalmar offers a ten-day terminal design sprint service, which is a tailored feasibility study that examines the options of electrification and automation deployment for your terminal. To learn more, please visit here or contact Christopher Saavedra directly at christopher.saavedra@kalmarglobal.com.
Related articles
Subscribe and receive updates in your email
Iscriviti alle nostre pubblicazioni