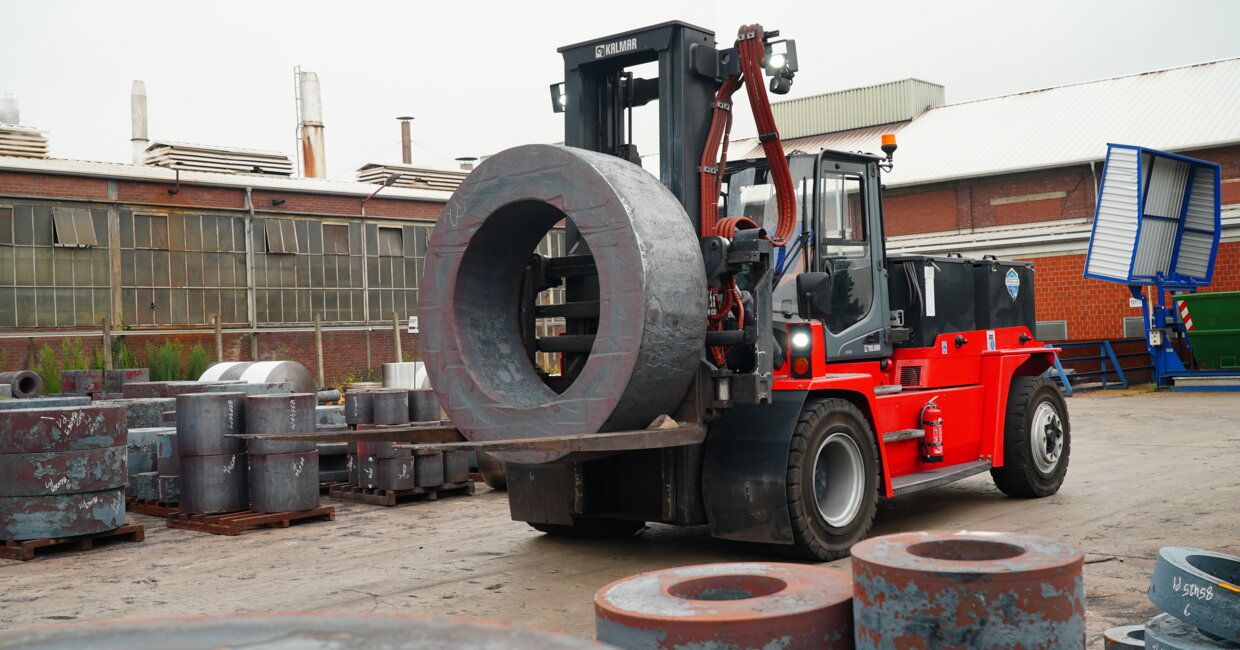
Change of traction: Electric Forklifts at the Erft
The Diederichs family has a blacksmith tradition that is around 400 years old. Since 1950, it runs the Hammerwerk Erft (HWE) in Bad Münstereifel in Germany. The owner-operated open-die forge has an excellent reputation and serves customers across Europe. The production of open-die forgings and seamless rolled rings are among the core competences. The product portfolio includes seamless rolled rings, shaping shafts, perforated discs and much more. Rods, shafts, hub discs or seamless rolled rings (available in over 100 materials) are used in shipbuilding and mechanical engineering, in gearboxes, wind power plants and in valve construction, amongst other things. Depending on the product type, the heaviest HWE components are aimed at a maximum diameter of 2800mm and weigh up to 20,000 kg.
The forklift fleet consists of 22 units, most of which have a load capacity of 5,000 kg. In 2012, the decision was made to equip the medium forklifts with electric drives. Kalmar is the supplier for the high-powered 8,000 and 16,000 kg payload electric forklifts from the current ECG series, which covers a payload range from 8,000 to 18,000 kg.
Frank Ueck manages the fleet at Hammerwerk Erft: "Sustainability, ergonomics and performance were the top priorities for the change of traction". The three electric Kalmar forklifts (2 x 8-tonne and one 16-tonne) are partially equipped with heat protection (protected hydraulic hoses, cylinder protection, enlarged front mudguards, central lubrication) to be used at the heating furnaces. An 8-tonne standard version without heat protection is used to load lorries. Heat, difficult visual conditions and travel distances of up to 800 m are typical parameters of use in this open-die forge. The EGO comfort cabin, reversing camera, BlueSpot and reversing alarm (white noise) are therefore important features.
David Odenthal is the responsible regional sales manager at Kalmar and designed the special units together with Frank Ueck. The e-forklifts are equipped with duplex masts with a lift height of 3,750 mm. The battery capacity of the 8-tonne forklift is 1,720Ah, while the 16-tonne forklift is equipped with two 120 V batteries and a total of 2,408Ah. The operational profile at HWE allows for the omission of exchangeable batteries. The new electric forklifts are charged in a specially created charging station with 2 x 63 A and 1 x 32 A respectively. "One battery charge is enough for two shifts with our operational profile", Ueck explains. Significantly higher ergonomics – due to noise reduction and performance on a par with diesel-powered forklifts – tipped the scales in favour of the "three red Swedes". Thanks to Kalmar Insight, the large forklifts can be monitored in real time. Data on vehicle condition, battery health, etc. are available online.
Special features of the Medium Electric Forklifts
The improved electronics of the electric equipment series are a fast, intelligent and stable system that makes the forklift user-friendly and reliable. The electronics require significantly fewer connection points and cables, reducing the frequency of errors and increasing operational reliability. The electronics include redundant CAN (Controller Area Network) bus technology. It monitors the status of all components in the driveline. The options are lead-acid and lithium-ion batteries. HWE opted for classic PzQ batteries. All data for condition monitoring is supplied by the CAN bus via a 3.5" display at eye level in the cabin. The variable pumps of the load-sensing hydraulics automatically sense the load during each operation and adjust the oil flow accordingly, enabling faster lifting cycles with reduced power consumption. Electrics and hydraulics are closely linked for shorter response times, faster lift speeds and increased control. This combination helps the driver to increase their productivity and reduce fuel consumption. Failures are reduced by cooling and maintaining cleanliness.
Related articles
Subscribe and receive updates in your email
Iscriviti alle nostre pubblicazioni