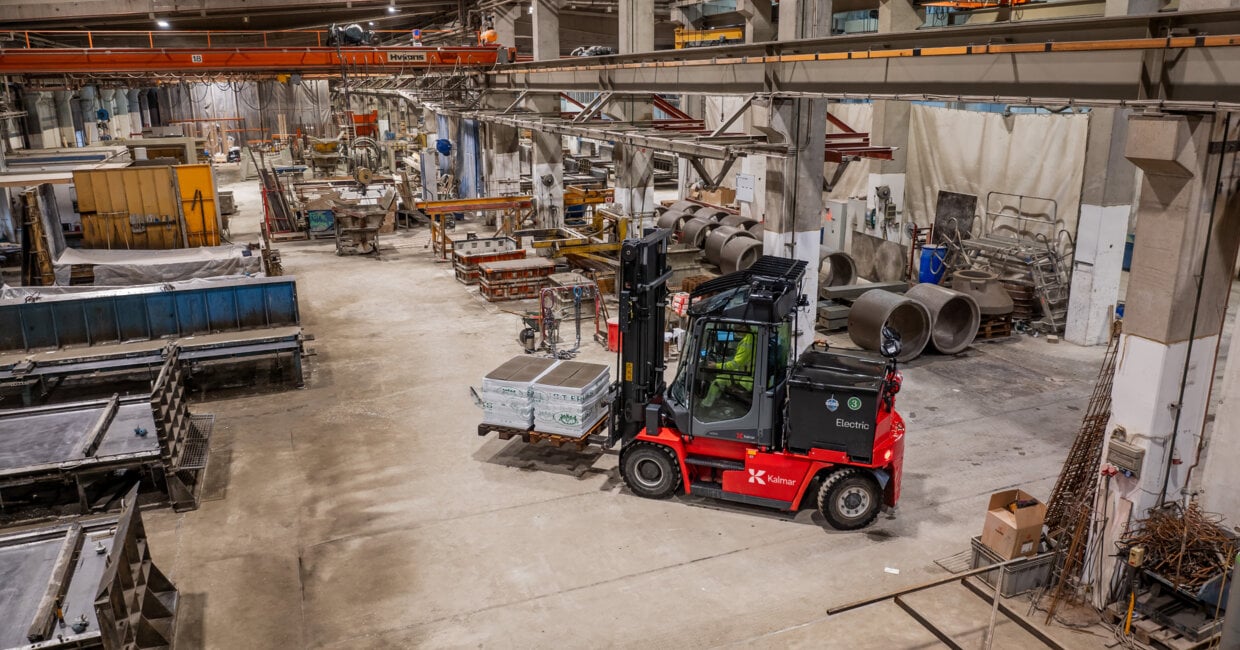
Light Electric Forklifts working like a dream for concrete product supplier S:t Eriks
Pushing for CO2 reduction, Sweden’s biggest concrete product manufacturer S:t Eriks took a bold step forward with seven Kalmar Light Electric Forklifts. After some initial skepticism, going electric proved to be the right choice in every way.
The biggest challenge for S:t Eriks is the CO2 footprint of their products, like paving stones and retaining walls, but that did not stop them from setting clear sustainability goals. They saw electric equipment as an essential step towards reaching their climate targets, and Kalmar was a natural choice for them.
“We have long experience with Kalmar diesel trucks and hoped to expand our collaboration with Kalmar,” says Daniel Rubin, Production Manager at S:t Eriks in Staffanstorp.
Across November and December 2022, S:t Eriks replaced seven of their eleven old diesel forklifts with Kalmar Light Electric Forklifts. Such a big change demonstrated great trust in Kalmar. With a full-service contract and regular communication, S:t Eriks now enjoys the support of Kalmar’s whole organisation.
Great lifting capacity and driver comfort
“S:t Eriks wanted to do this with someone who knows how to maintain electric forklifts, how the batteries should be treated, and how the drivers should handle the forklifts,” explains Eric Wass, Sales Representative at Kalmar Sweden.
With a full-service contract and regular communication, S:t Eriks now enjoys the support of Kalmar’s whole organisation.
“With Kalmar’s preventive maintenance, we can rely on the trucks and focus on our operations,” Rubin says.
As is often the case when shifting to electric equipment, there was some initial skepticism from drivers. Could electric forklifts really do the job? Why change something that already works? But with first-hand driving experience and training from Kalmar, the drivers were won over.
“The biggest pro with the electric forklift compared to the old one is the lifting capacity.”
Nabil Aysef, a forklift operator at S:t Eriks, describes driving an electric forklift as a wonderful feeling, thanks to the highly ergonomic cabin adjustment features and reduced noise levels.
“The biggest pro with the electric forklift compared to the old one is the lifting capacity. Now I just push a button, and the truck does the rest,” Aysef says.
The key thing with electric forklifts is taking proper care of it, and now, the drivers at S:t Eriks know exactly how to do that. They were given extensive instructions by Kalmar on how to make the battery last and how to charge it correctly.
Narrow chassis for agile operation
Kalmar has been producing Light Electric Forklifts with Lead Acid batteries for over 35 years. This experience provides numerous business benefits, including higher equipment availability with reduced need for maintenance.
“Perhaps the biggest difference between now and five to seven years ago is that previously these forklifts were mainly used indoors. Now customers use them outdoors as well, so they are totally replacing the diesel segment,” Wass says.
A clear benefit of Kalmar’s Light Electric Forklift for S:t Eriks, who mainly work outside in their yard, is the uniquely narrow 1600 mm chassis and small turning radius. This is something that competitors were not able to match.
But how does an electric machine handle the dust and dirt involved in concrete production?
“As long as you keep the forklift clean and do your daily check-ups, it will work efficiently. We also put some extra rubber protection plates behind the lifting mast to protect critical components from dust,” Wass explains.
“The acceleration is great, you get full speed in an instant, which makes it perfect for loading and unloading trucks.”
Suitable to replace diesel anywhere
Wass considers the Light Electric Forklift suitable for use in practically any industry, in any environment.
“They are reliable. The acceleration is great, you get full speed in an instant, which makes it perfect for loading and unloading trucks. The only thing that is perhaps missing is the top speed. But how many times per day do you really utilise the top speed with a maximum load?”
Very few, actually, as evidenced by the wealth of data on equipment use provided by our Kalmar Insight performance management tool.
With all the evident benefits, what is holding customers back from switching to diesel? Often the answer is investment cost, which can be higher compared to diesel.
“You have to do a TCO calculation: the more hours you drive, the faster you will break even. In normal cases it’s a no-brainer. You look at five years driving 1500 hours a year, you will break even in one-and-a-half to two years maybe, then on you will earn money,” Wass says.
For S:t Eriks, the plan is to go ahead and replace their remaining diesel forklifts with electric ones.
“Our target for the future is to keep reducing our CO2 footprint and contribute to a sustainable society,” Rubin says. “It feels good doing this with Kalmar.”
Related articles
Further reading
Subscribe and receive updates in your email
Iscriviti alle nostre pubblicazioni