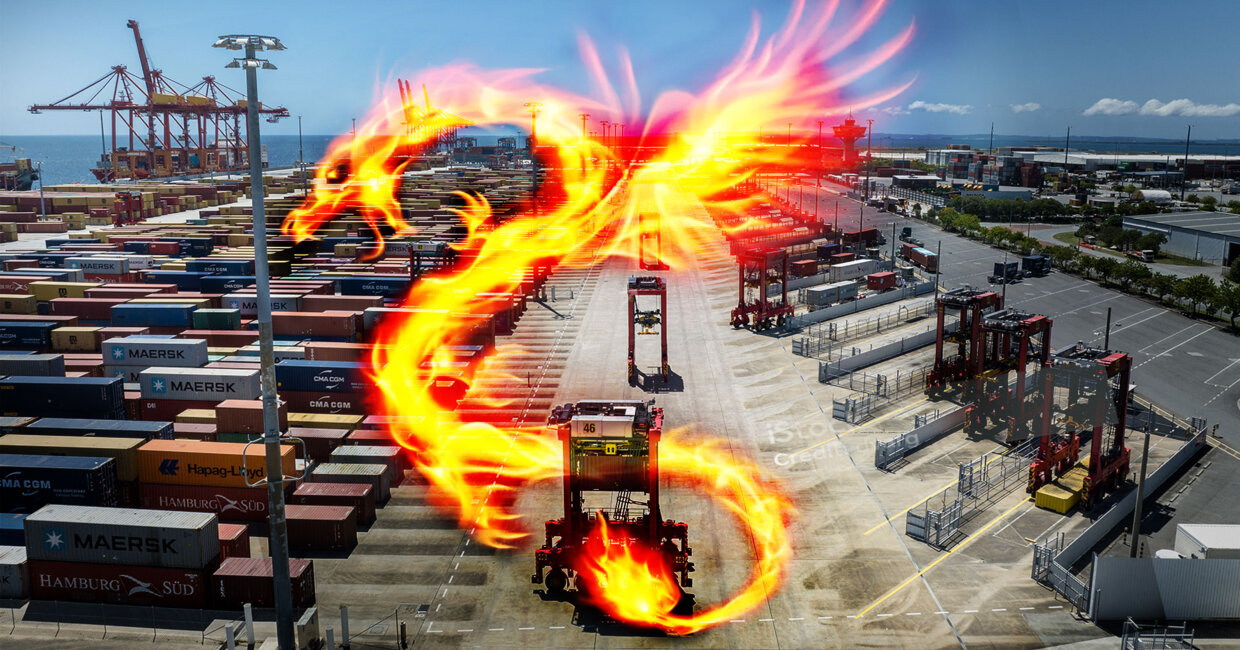
Myth #1: Automated Straddle Carrier Terminals Are Too Expensive
We've all heard the argument. Automated straddle carrier terminals have a high total cost of ownership. All those complicated systems are too expensive to develop and to maintain. In terms of TCO, the traditional ASC concept is still unbeatable. Right?
Wrong. Both real-world customer data and the latest modeling and emulation results show that the Kalmar AutoStrad™ is the most economical automated handling concept for almost any container terminal. The cost difference is especially dramatic when compared to traditional yard crane concepts.
So what is TCO, anyway?
Total Cost of Ownership (TCO) has a significant role in automation investments. It is no secret that the upfront investments for automation are significantly higher than for manual equipment. However, what the investment offers is significant cost savings and – more importantly – clear visibility to future operations. In an automated environment, business can keep going around the clock, even during the times that would be most expensive for a manual terminal.
TCO comparisons between a manual straddle carrier operation and the Kalmar AutoStrad™ concept will almost certainly favour the AutoStrad™ in high labour cost areas where the terminal operates at high intensity. Investing in automated straddle carriers means a higher capital expenditure but lower operating costs; however, the larger initial investment also offers a longer equipment lifetime as the automated straddle carrier is not subject to the same wear and tear as manual equipment.
Even in hybrid yard crane concepts in which a fleet of automated straddle carriers serves an ASC block, automated straddle carriers provide a lower TCO compared with AGVs. The cost of an individual machine is slightly higher for automated straddle carriers over AGVs, but automated straddle carriers will be able to serve a given number of cranes with a much smaller equipment fleet. This is because straddle carriers enable fully decoupled operations, in which containers can be deposited on the ground without the need to have a specific machine always available to receive the container from the quay or ASC cranes.
Automated straddle carriers also eliminate the need for double trolley quay cranes which are required for loading and unloading containers on AGVs. This can bring savings of several million euros on the just cost of the quay crane and its support infrastructure.
TCO for Manual Straddle Carrier vs. Automated Straddle Carrier
To ensure the comparability of different solutions, we prefer to use the CapEx and OpEx cost split as well Equivalent Annual Cost (EAC) that annualizes the CapEx for each solution factoring in the cost of capital, equipment lifetimes as well as annual OpEx costs.
Our example calculation for manual straddle carriers reflects the conditions of a European container terminal with ten ship-to-shore cranes. The EAC analysis assumes a weighted average cost of capital of 10% and an equipment lifetime of 12 years for the manual straddles and 15 years for the AutoStrad™.
In this scenario, the AutoStrad™ offers annual cost savings of over 13 % when compared to the manual straddle carrier operation. However, it is important to note that this number can be significantly higher for terminals in North America or Oceania. The cash flow profile differs quite significantly from a manual straddle carrier, as CapEx is around 2 x higher, but OpEx is over 50 % lower.
Total Cost of Ownership: Automated Straddle Carrier vs. ASC
The Automated Straddle Carrier offers terminal operators an automation system that is light in infrastructure compared to an Automatic Stacking Crane. It is necessary to state that in return for the higher capital investment of the ASC, it does offer a longer lifetime than the AutoStrad™, but the breakeven for the investment will be further in the future.
Our example again assumes a European container terminal with ten STS cranes and a weighted average cost of capital of 10%. Equipment lifetimes are calculated at 15 years for the AutoStrad™, 25 years for the ASC and 20 years for the AGVs serving the crane.
On a comparable basis, the Automated Straddle Carriers offers more than 35 % lower annual costs than the ASC solution. This difference is mostly attributed to the significantly higher CapEx of the ASC due to the larger required infrastructure and the need to have two container handling systems, one for stacking and one for horizontal transportation. This leads to a larger fleet of container handling equipment, which is reflected in CapEx costs.
Doing the math
Automation offers clear financial advantages, but the exact numbers should be calculated taking into account the terminal operator’s cost structure. The terminal is the best expert on its own operations, and automation projects always revolve around a basic wishlist – an idealised implementation that encompasses the swiftest possible deployment, maximum performance improvement, and an integrated turnkey solution.
Success in practice (and ultimately that all-important Total Cost of Ownership) will depend on skilful optimisation of these and numerous other factors. In addition to the benefits detailed above, automated straddle carriers bring savings from significantly reduced safety and accident costs, less unplanned maintenance, and easier maintenance with only one type of equipment. When comparing various terminal concepts, the AutoStrad™ system is by far the most economical option both in terms of capital investments and lifetime costs.
Related articles
Further reading
Subscribe and receive updates in your email
Iscriviti alle nostre pubblicazioni